3D-printing solutions for jigs and fixtures
Stratasys 3D printing for jigs and fixtures
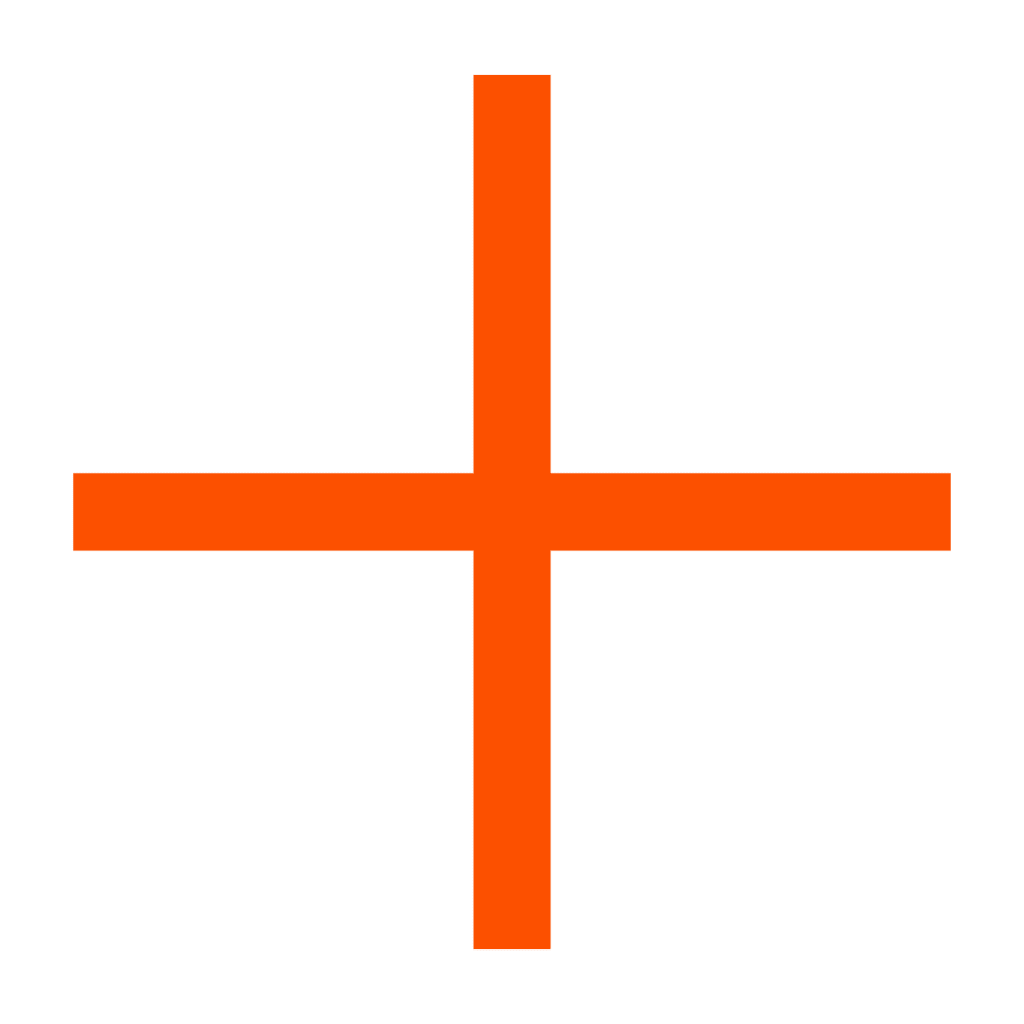
Why use 3D-printing technology for jigs and fixtures?
To maintain production quality, efficiency and safety, businesses rely on highly customised jigs and fixtures to position, hold, protect and organise components and sub-assemblies at all stages of the manufacturing process.
3D printed assembly fixtures can significantly enhance production of tools and aids, helping to eliminate cost and design barriers and amplifying turnout.
FDM 3D-printing technology builds up plastic parts layer by layer directly from CAD files, simplifying the fabrication process. Tool making becomes less expensive and less time-consuming.
Putting performance first
FDM places fewer constraints on tool configuration, meaning tools can be crafted for optimal performance and ergonomics. Jigs and fixtures made from durable thermoplastics are tough but lightweight and able to withstand rugged manufacturing environments
Multiple materials
Multi-material capabilities of PolyJet technology allow for highly bespoke jigs and fixtures, dependent on need – making jigs, fixtures and workholdings with additive manufacturing ideal for any industry.. Biocompatible options make them perfect for the medical industry also.
In demand printing
Create digital inventories for on-demand printing, rather than storing manufacturing tools when they are not in service. Digitalising your inventory means quicker, more flexible decisions and an ability to tweak designs from a huge existing inventory of jigs and fixtures.
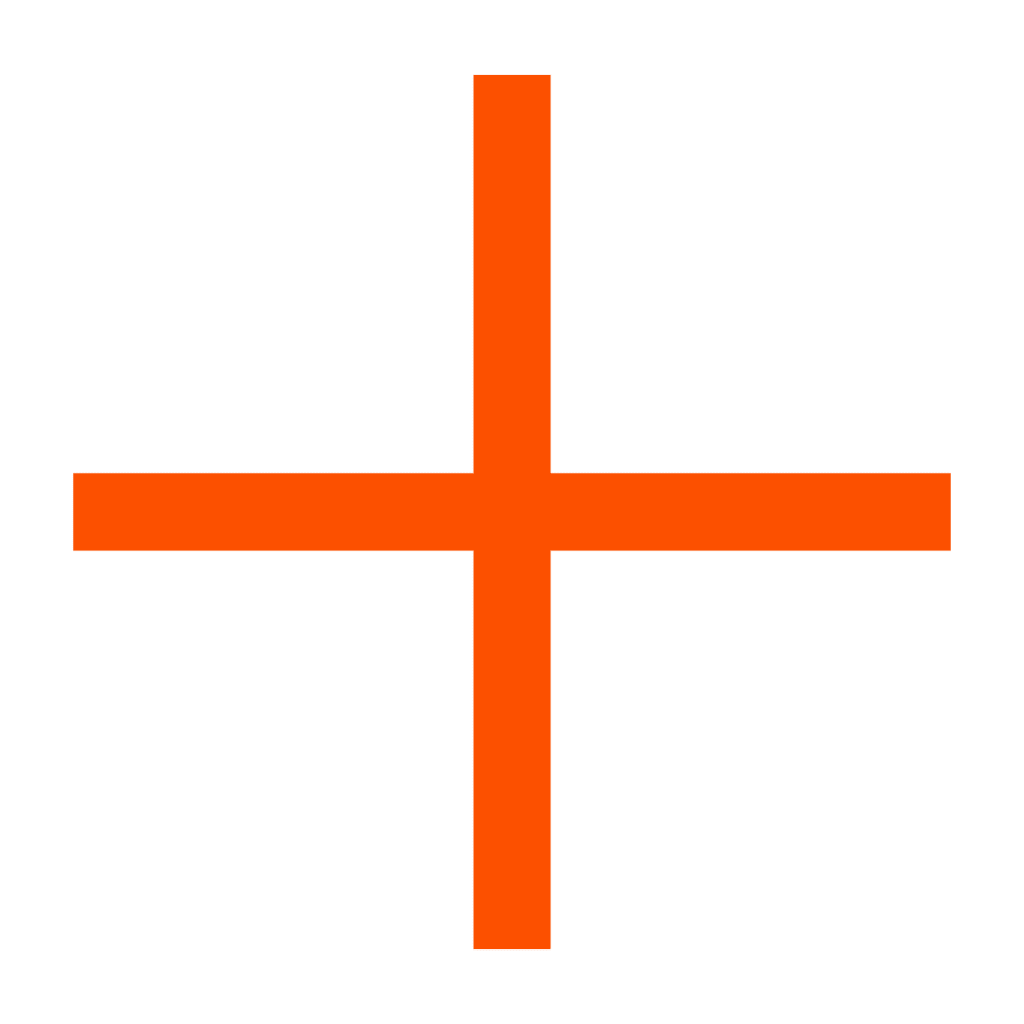
Creating jigs and fixtures with additive manufacturing
Stratasys technology is revolutionising the way products are manufactured. With additive manufacturing, engineers can create jigs and fixtures with complex shapes quickly and easily.
Traditional methods of manufacturing are often slow and expensive because they require extensive planning to create moulds for each part. 3D printing technology eliminates the long lead times of conventional manufacturing methods by enabling manufacturers to create and print custom jigs and fixtures quickly and cost effectively.
Engineers can 3D print jigs and fixtures for a number of applications, including welding and cutting, painting, quality control testing, assembly, and more. For example, 3D printed fixtures can be used to improve assembly quality and accuracy in a variety of industries, including automotive, aerospace, and medical.
3D printing assembly fixtures is helping to improve the efficiency and reliability of manufacturing processes for a range of industries, including automotive, medical, aerospace and manufacturing.
3D printing jigs and fixtures can be done easily, quickly and cost-effectively on-site.
- Prototyping existing jigs and fixtures with 3D printing enables you to create design changes before ordering production parts – reducing lead time and costs.
- Custom designs can be used for various applications, such as welding and cutting, painting, quality control testing, assembly and more.
- For low volume, complex or precision applications including for 3D printing fixtures and workholdings, in addition to jigs and tooling, the method offers a cost-effective solution compared to traditional methods.
- Boosts repeatability and reduces scrap costs due to superior tolerance control.
- Available in a wide range of materials to suit different product requirements.
- The fit and finish is impeccable – helping to achieve tight tolerances that are vital to product quality.