Named one of the UK’s Top 40 universities in the Guardian University Guide 2025, the University of Sunderland has long been at the forefront of higher education and cutting-edge research.
Its state-of-the-art facilities in the David Goldman Technology Centre, including an additive manufacturing centre of excellence, position the university as a leader in engineering education.
A partnership with SYS Systems, UK Platinum Partner for Stratasys, has enabled the institution to equip students with the tools and skills they need to become problem-solving, technically adept engineers ready for industry challenges.
Project Brief:
To remain competitive among the UK’s top universities, the University of Sunderland continually invests in the best facilities and equipment.
The School of Computer Science and Engineering has been a long-standing advocate of 3D printing technology but recognised the need to elevate its capabilities to maintain its status and attract high-achieving students.
Dave Knapton, Associate Head of School – Computer Science and Engineering, said: “Here at the University of Sunderland, students can expect a very contemporary education experience.
“We teach traditional engineering programs, but also the latest and current digital technologies, trying to train students to be able to develop a more sustainable world.
“The university has had 3D printing capabilities for a long, long time but the recent investment in the very best technology really shows itself in the materials that we can now print, and also the quality of those prints.”
The university’s goal was clear: to integrate the latest advanced systems to showcase the very best in 3D printing technologies and provide students with an unparalleled learning environment.
The Solution:
To meet its goals, the University of Sunderland partnered with SYS Systems, a leading provider of Stratasys 3D printing technology. The university began with a Stratasys J850 PolyJet printer and has since expanded its capabilities with three additional systems, each offering unique benefits.
Dr Spyros Fakiridis, Lecturer in Engineering, said: “The fact that we have four machines here at the University of Sunderland proves that our relationship with SYS Systems has been positive and that we’re only looking to extend that relationship further.”
The printers include the Fortus 450, the world’s most popular industrial FDM 3D printer, which enables the production of durable, end-use parts with precision, the F770, a large-format FDM 3D printer which offers increased printing flexibility and the option for more extensive projects, the J850, a multi-colour, multi-material 3D printer offering unparalleled accuracy and surface finish, and the Origin, specialised in high-performance materials such as elastomers and medical-grade polymers.
This comprehensive set-up supports a variety of applications, from student projects to research initiatives and collaborations with industry partners.
The Benefits:
The benefits of incorporating Stratasys 3D printing technologies into the university’s curriculum are both immediate and far-reaching.
The machines can produce production-grade parts, with an advanced selection of material choices across the four different machines providing flexibility, but also highlighting to students how cost-effective and efficient 3D printing is when compared to traditional methods.
Dave said: “The beauty of working at a place like the university is you never know what that next project is going to be. We can now see 3D printing used in many, many different sectors.
“These machines offer access to much more technical materials, so we’re getting production realistic parts without the expensive tooling costs and the lead times that are involved in more traditional methods.
“The things we can now print were just unforeseeable a few years ago. So that’s where the advances are and I think that’s where the advances in technology will continue.”
The hands-on experience that students are able to gain with industrial-grade equipment sets them up for a future in engineering, with more and more manufacturers turning to 3D printing to gain an advantage. By having access to such technology as the Stratasys machines, students can themselves gain an edge in terms of their employability and prepare them for real-world challenges.
Dr Aidan Bowes, Engineering Lecturer and Programme Leader, said: “I think it’s a really rare thing to have this many Stratasys machines all under one roof.
“It’s hugely important for students to have access to machines like these, it allows them to develop a little bit further, rather than just using cheap, basic 3D printers. They can actually do more complex design work that can push the limits of their design using these machines a little bit further and makes it work a little bit better as well.”
Its not just the benefits to the students that the university profits from, with the Stratasys technology creating broader opportunities to support advanced research, develop industry partnerships and engage with local businesses.
Dr Bowes added: “We’ve got a really good opportunity with the machines here. It’s a great thing for the students to have access to. It really increases the things that they can do on their course, but also it’s been really good for working with local businesses, working with people who might want to get involved with additive manufacturing but not know where to start.
“It really sets us up as a centre of excellence and allows us to work with industrial partners and do additional research work and commercial work, so it’s a really beneficial thing to have.”
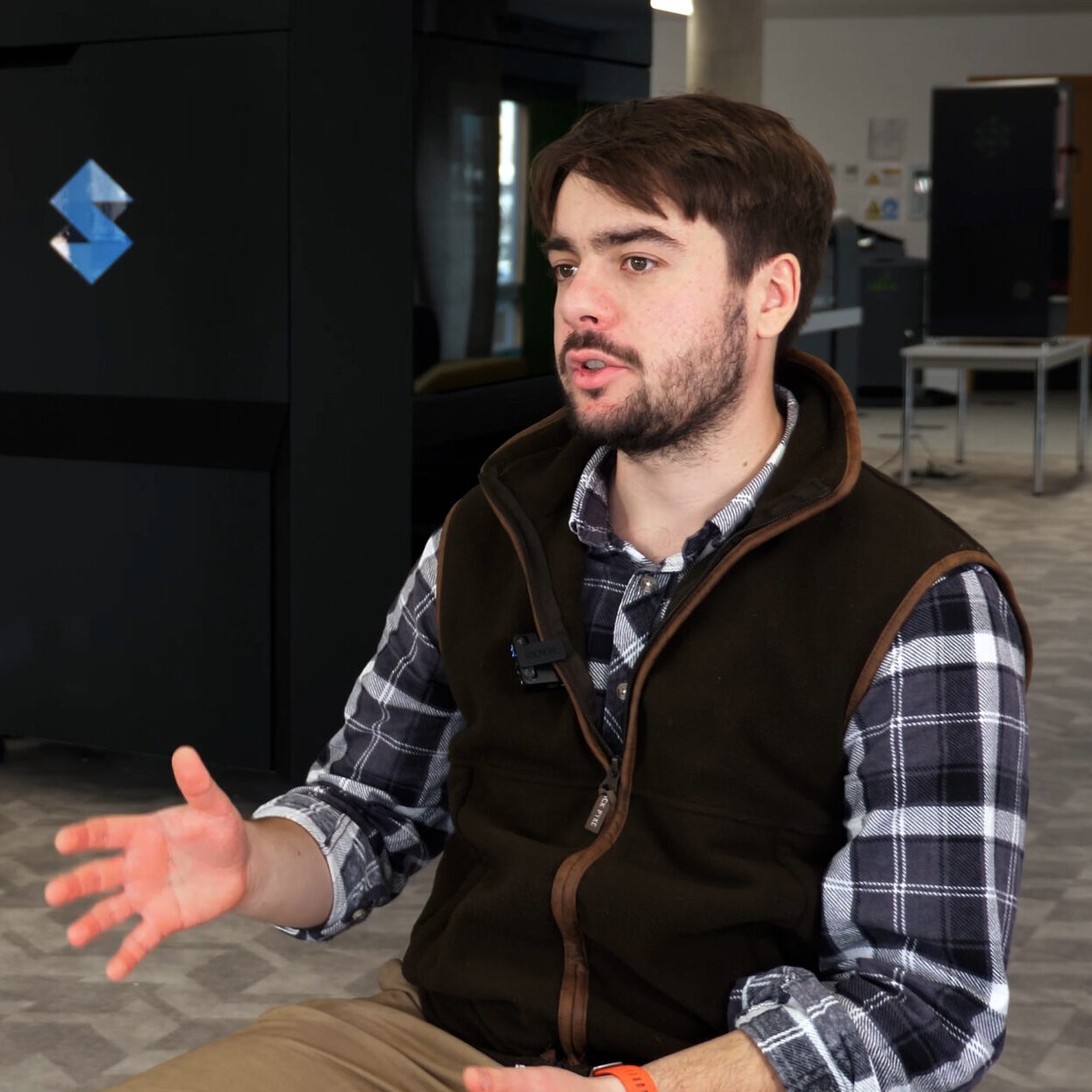
Why SYS Systems?
The University of Sunderland’s partnership with SYS Systems has enabled it to create a cutting-edge centre of excellence for additive manufacturing.
But the relationship extends beyond supplying 3D printers, with the training, support and overall experience provided by SYS Systems making the difference and providing the university with confidence to return as a repeat customer.
Dave said: “The partnership with SYS Systems is really important because it allows a much broader experience of the full digital workflow that industry expects and uses; the kit here is a really important part of that.
“For those looking to invest in the latest technology, we found the partnership with SYS Systems to be really beneficial. It’s not just buying a machine, but the training package that goes alongside that, the aftercare and support, the access to new materials and new technologies as they come along; that’s why we were pleased to expand the range after our initial investment.”