The modern automotive industry constantly needs to work more efficiently, test more thoroughly and ensure full confidence in their production processes. Automotive companies require materials that are strong, durable, lightweight and that can achieve increasingly complex geometries.
The automotive industry is producing an increasing amount of customised, specialist features for vehicles and more and more companies are turning to FDM 3D printing to help support their processes. FDM 3D printing provides a fast, flexible and high-quality manufacturing solution that ensures automotive companies can meet the fast and demanding challenges of the industry. Many of the world’s biggest automotive companies are turning to additive manufacturing to make manufacturing faster, more cost effective and flexible, including Porsche, Jaguar Land Rover and Peugeot.
SYS Systems is the platinum partner of Stratasys in the UK, supplying and supporting the full range of world-renowned 3D printing technologies from prototyping through to production. SYS Systems provides world renowned Stratasys 3D printing technologies to enable automotive companies to build durable concept models, prototypes, tooling and end-use parts on-site.
Why FDM 3D printing is vital to automotive companies
- Rapid Prototyping
FDM technology provides a rapid prototyping solution for the automotive industry, facilitating fast and efficient product testing and iterations, without the high costs associated with traditional prototyping methods and outsourcing. Rapid prototyping enables automotive companies to experiment with ideas and concepts, producing examples and proof of concepts within a product development cycle.
- Improved design capabilities
The use of FDM 3D printing technology has unlocked the design capabilities of automotive companies, allowing them to develop and produce more complex and innovative products, that would have been impossible using traditional manufacturing methods.
- Customised 3D printed parts
FDM 3D printing allows automotive companies to produce customised products for individual customers, such as customised dashboard designs, ergonomic seat structures and personalised in-car accessories tailored to specific drivers increases.
- Lightweight materials
FDM technology uses lightweight materials including engineered plastics and composites to significantly reduce the weight of vehicles, improving fuel efficiency and reducing automotive emissions. For example, advanced rubber-like materials can be used to develop door seals, gaskets, and shock absorption components, translucent materials can be used for fluid analysis, and acrylic-like materials can be used to replicate dashboard components.
- Increased efficiency
FDM 3D printing has drastically increased the efficiency of automotive companies by reducing production time, increasing manufacturing flexibility, and enabling on-demand production. FDM 3D printers can produce a wide variety of automotive parts, from simple prototypes to more complex end-use components. The ability to store and easily reprint previous designs and builds dramatically speeds up production variation without the need for expensive tooling or lengthy changeovers.
- Cost effective
Traditional manufacturing methods often require expensive tooling and machinery costs. FDM 3D printing offers a more cost-effective solution, allowing automotive companies to produce prototypes and products in-house, as well as enabling small batch and on-demand production without the need to invest in expensive tooling.
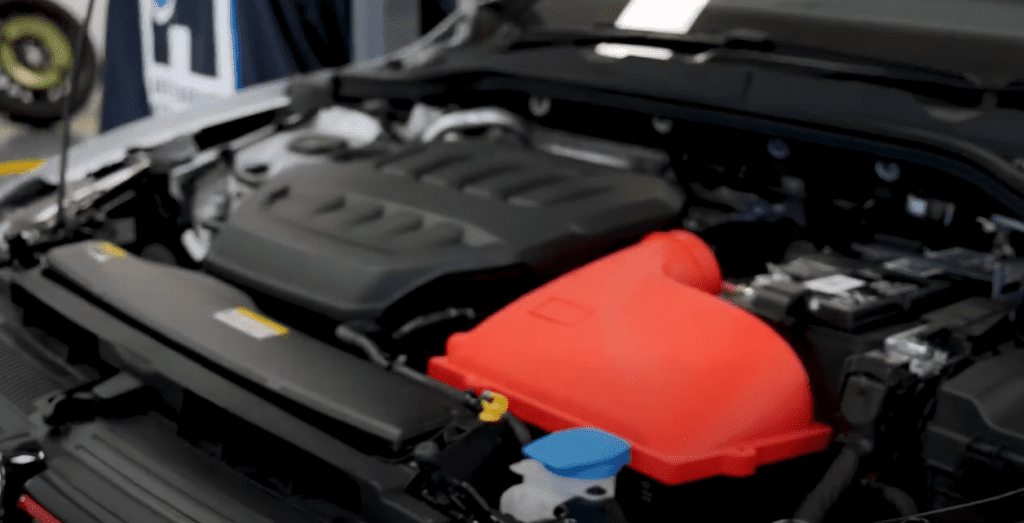
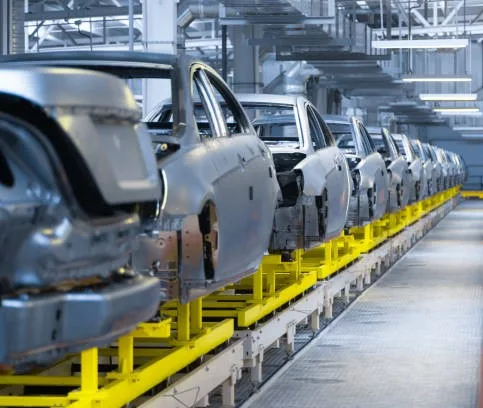
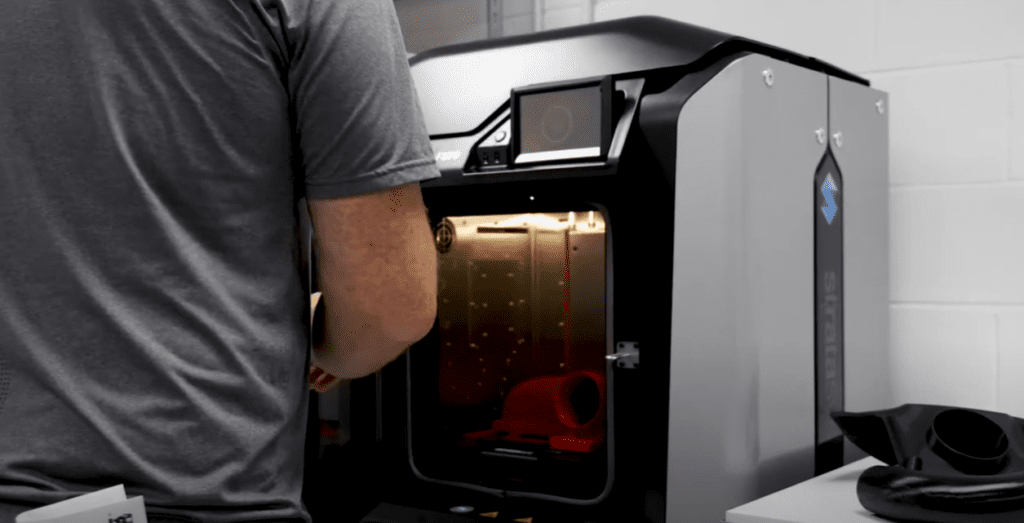