What is SLA 3D printing?
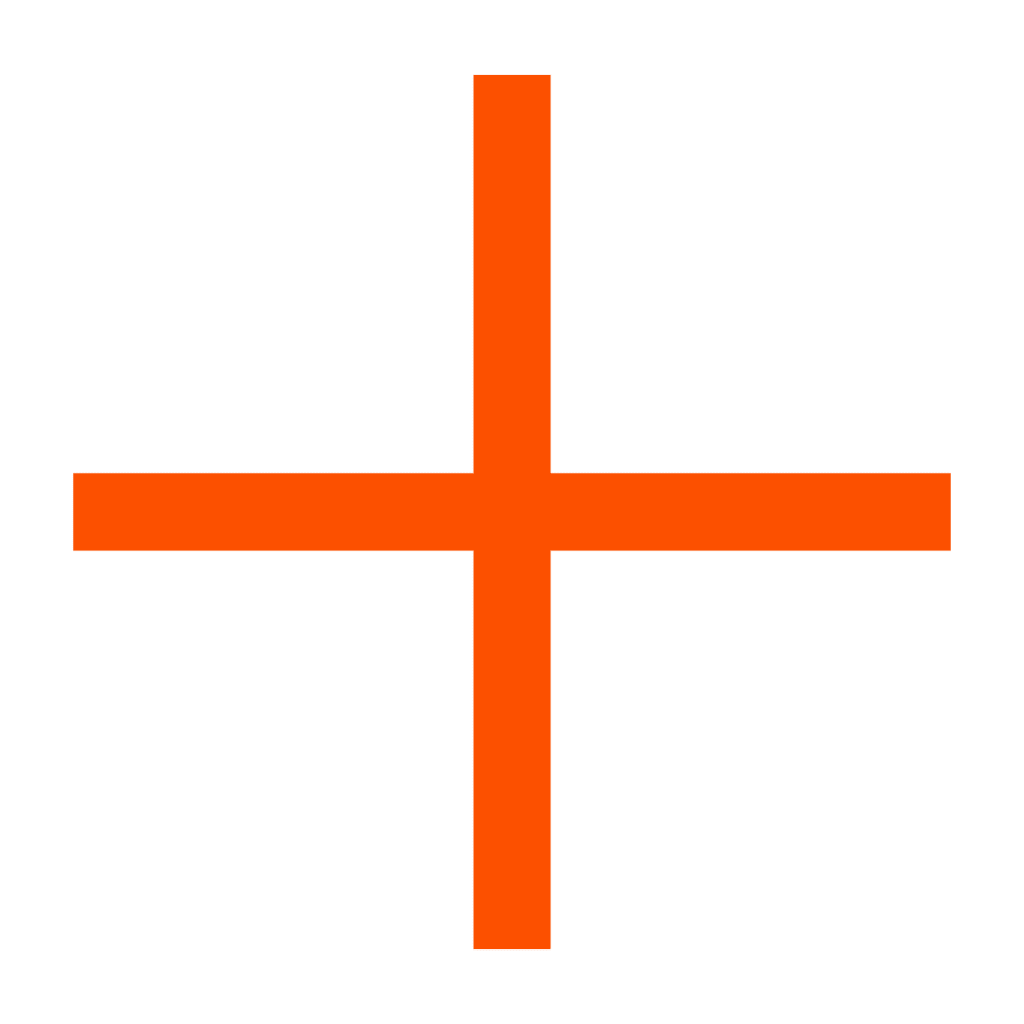
Stratasys Neo stereolithography 3D printers produce highly-accurate parts with unparalleled industry quality. The Stratasys Neo is a reliable, stable system, proven in high-pressure working environments like service bureaus and F1 that require quick turnarounds.
Users of legacy stereolithography (SLA) 3D printers are often challenged with producing high-quality, accurate 3D printed parts for prototyping or tooling applications. Parts produced on legacy stereolithography 3D printers can at times be inaccurate, requiring lengthy finishing which increases time and costs.
Companies are upgrading to the Stratasys Neo SLA printer series to produce 3D printed parts with outstanding sidewall quality, detail, accuracy and extremely small variability from part to part.
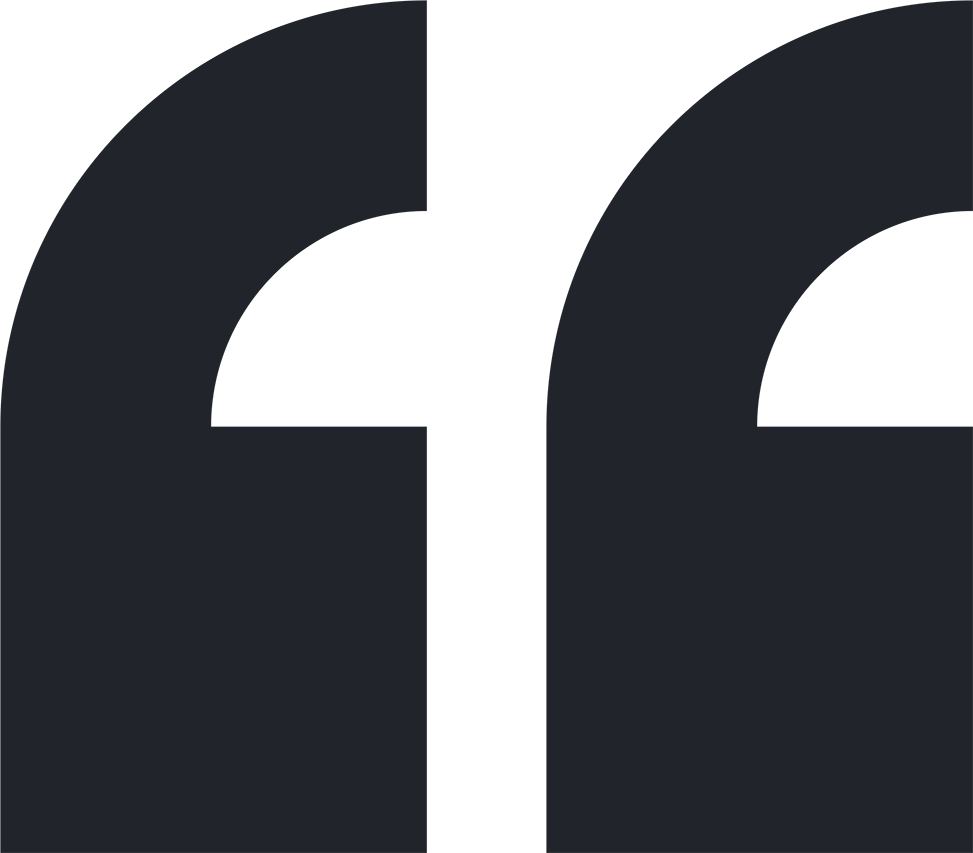
The Neo800 is very much at the heart of our vehicle development process, from design to production.
Tim Chapman - McLaren Racing
Key benefits of Neo Stereolithography industrial-grade technology
50% finish time
Reducing the finish time of parts by up to 50%, the Neo produces highly-accurate parts with unparalleled industry quality with exceptional sidewalls and crisp feature resolution.
Open resin system
An open material system means users are not restricted by the usual parameter constraints, offering the ability to utilise any 355 nm hybrid resin chemistry.
Proven reliability
Designed by engineers for engineers, the Neo is carefully engineered throughout using state-of-the-art technology, proven components and aesthetic finishes.
Titanium software
Titanium is an easy-to-use software interface which allows users to start builds quickly and monitor throughout the building process.
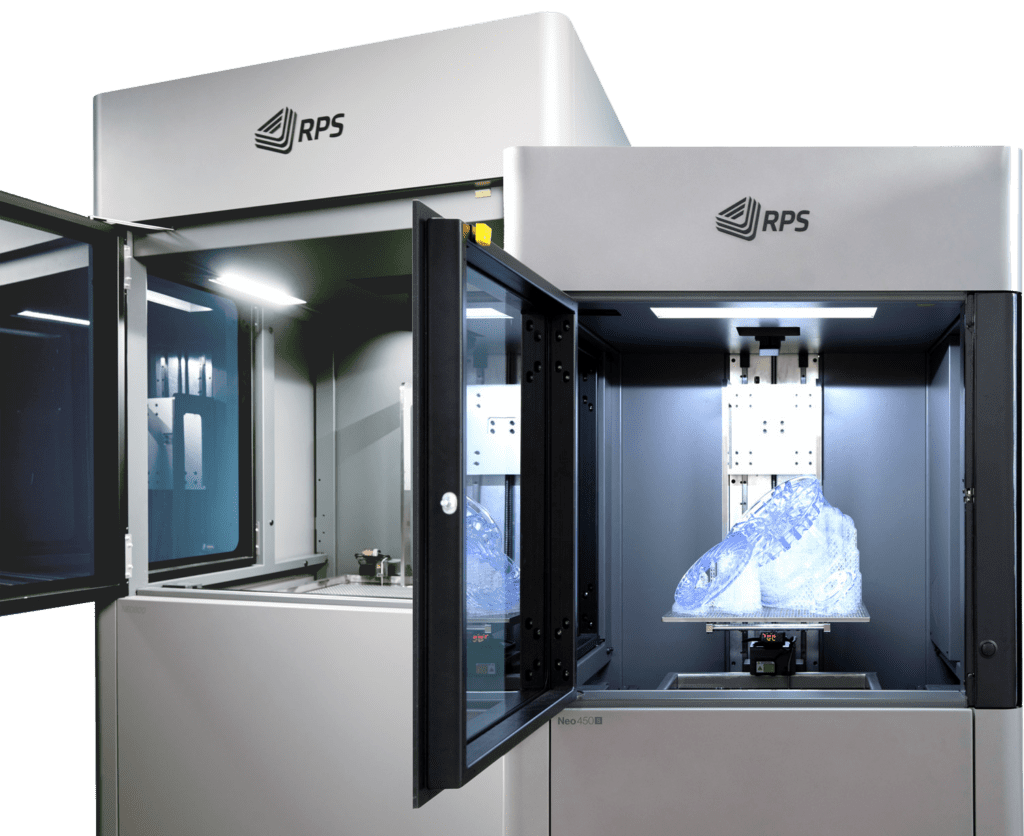
SLA FAQs
SLA 3D printing works by depositing successive layers of material on top of one another like a stack of pancakes. A UV laser then scans over the resin to form the individual layers. When the process is complete, your object will have emerged with a stunning three-dimensional finish.
A basic SLA print takes anywhere from 4 to 24 hours depending on size and complexity. If you need reduce time part part, you can run multiple parts simultaneously and drastically reduce the amount of time it takes to print each individual part.
SLA can be used as a supplement to existing manufacturing processes, creating workholdings and tooling with a high degree of accuracy. It is also ideal for functional prototyping, where testing is paramount.
Resin is a type of plastic that is used in SLA 3D printers. It is applied in a liquid form before being cured by a UV laser to create the object layer by layer. There are many different varieties of resin available with different properties; each one can produce a different effect in the final printed object. Depending on the resin chosen, you can produce highly-detailed models with smooth surfaces and various mechanical properties, as well as transparent or opaque objects.
Yes. Depending on the end use you may need to do more, or less post processing. This could be as simple as removing any support material and washing the part in a solution to remove excess resin. But could include sanding, polishing and painting depending on the demands of the part.
The maximum size that can be printed in one pass depends on the size and shape of the build platform. The largest size offered by Neo is 800 × 800 × 600 mm.
You can typically achieve a resolution of around 20 microns using SLA printing. This is finer than the resolution produced by FDM printers.
Somos® ProtoGen 18420 - Flexible engineering-grade thermoplastic.
Somos® WaterClear Ultra 10122 - Used in mechanical parts because it is tough and durable with good impact resistance.
Somos® WaterShed XC 11122 - Low viscosity resin that resists sagging and exhibits good strength when cured.
Somos® NeXt - High-conductivity, low-odour material that offers excellent mechanical strength and easy machinability after printing.