In today’s manufacturing landscape, product and part requirements are becoming increasingly intricate and customised, leaving traditional low-volume production methods no longer cost-effective for manufacturers.
The high costs associated with tooling, re-tooling, and support materials for low-volume production runs struggle to meet the needs of customers who are seeking adaptability, flexibility, and on-demand production.
3D printing offers a revolutionary solution to bridge the gap for low-volume, high-value products by removing the constraints of traditional low-volume manufacturing methods.
Eliminating the need for expensive tooling, minimising material waste, and enabling on-demand manufacturing, 3D printing offers a comprehensive solution for manufacturers seeking to cost-effectively produce low-volume, high-value products.
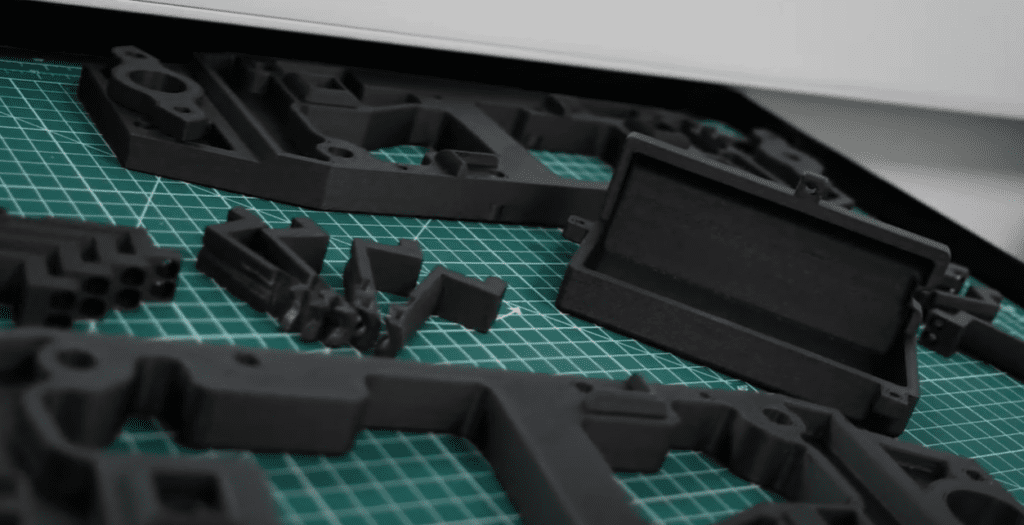
SYS Systems is the UK’s dedicated Platinum Partner to Stratasys, the world’s biggest commercial 3D printing brand. They provide the most advanced 3D printing technologies in the world, delivering a cost-effective solution for low-volume, high value production.
Stratasys 3D printers reduce waste by only printing the material needed for each part, unlike traditional subtractive manufacturing methods. This, combined with the elimination of expensive tooling and large inventories, allows manufacturers to adopt an on-demand production model, printing parts as needed and minimising inventory costs.
Stratasys’ wide range of robust materials enables the production of high-performance, end-use parts that can withstand even the most demanding environments, while the user-friendly software allows manufacturers to store and modify existing designs to allow for fast iteration and adaptation of products.
Explore how SYS Systems customers are utilising Stratasys 3D printing technology for low-volume, high-value production below:
Spectra Group
Spectra Group, a leading provider of specialised defence and military equipment, was challenged with the need to replace a critical, low-volume component needed, but the traditional route – injection moulding – would have cost them £15,000 for six units.
By investing in a Stratasys Origin One 3D printer, Spectra Group can now design, print, and deliver mission-critical components on-demand, creating a more streamlined process, with minimal post-processing, and accelerated production.
Spectra Group’s Head of Research & Development, Simon Perrett, explained: “It was for a part which we already had but we had no more left on the shelf. We asked the company that normally injection moulded these parts and new tooling was £15,000. The order was only for six. It was at that point I decided this was going to be our first project.
“With the Origin One, once we’re happy with a product, we don’t have to go and get any injection mould tooling or anything. We can literally produce a part, do a little bit of post-processing, insert all the parts we need to and then ship the product out. That was the revolution we were after and now we have achieved it.”
HellermannTyton
HellermannTyton, a leader in fastening and cable management solutions, faced the challenge of traditional end-of-arm tooling being bulky, expensive, and slow to produce.
By investing in the Stratasys’ Fortus 450 3D printer from SYS Systems, HellermannTyton can now design, print, and install lightweight, cost-effective end-of-arm tools overnight, reducing lead times by over 50% and tooling costs by over 75%, allowing them to seamlessly shift between standard and unique products, maximising their flexibility and responsiveness.
HellermannTyton’s Automation Team Leader, Dean Pentney explained: “Our previous end-of-arm tools were quite heavy, they took a long time to produce and they were also considerably high priced.
“With the traditional processes we would have to take an issue back to the supplier to propose a redesign, cost and then initiate an order. That process can take four weeks at best.
“With the Fortus 450, we saw a redesign of the end-of-arm tooling in an afternoon, printed it overnight and could install it the next day. We are typically looking at weight savings and lead time reductions of up to 50%, and cost reductions of up to 75%.”
Fluxaxis
Fluxaxis, a robust industrial materials and large-scale sculpture builders, were faced with translating artist Jam Sutton’s “David and Goliath” sculpture into a public exhibition, but their traditional construction methods were limited.
By investing in both a Stratasys F900 and a Fortus 250 3D printer, Fluxaxis can create large, complex sculptures with meticulous precision, capturing every intricate texture and expression and bringing Sutton’s vision to life.
Jake Augur, Fluxaxis Production Manager said: “When it comes to engineering, Fortus technology offers a more bespoke and accurate replica for a client’s needs. We can now produce parts which are both large and highly detailed in a multitude of layouts and materials.”