In the aerospace industry, manufacturers are tasked with designing and building high-precision, safety-critical components, leaving no margin for error. For aerospace companies, FDM 3D printing provides a fast, flexible and high-quality manufacturing solution that ensures they can meet the demanding challenges of the aerospace industry.
The aerospace industry has a relatively low production volume and high level of specialised components, making FDM 3D printing a perfect fit for aerospace companies.
Fused deposition modelling (FDM) is a popular 3D printing technology that builds products and prototypes layer by layer from the bottom up by heating and extruding thermoplastic filament. FDM 3D printing is designed for industrial applications, playing a crucial role in the manufacturing and production of aerospace components. It produces prototypes, functional parts, and complex geometries to meet the tight tolerances required from the aerospace industry.
Why FDM 3D printing is vital to aerospace companies
- Rapid prototyping and manufacturing:
FDM 3D printing helps cut product cycle times and accelerate product time-to-market by enabling rapid prototyping. FDM 3D printing allows for quick iterations and refinements, as well as faster manufacturing timescales and significant reductions in lead times. The speed of FDM 3D printing technologies can greatly accelerates the design and implementation of aerospace tooling, such as drill guides and other fixtures. This is essential for developing and testing safety-critical aerospace components before production.
- Customisation and complexity:
Aerospace components require complex and precise geometries. FDM 3D printing can create realistic prototypes and intricate, lightweight structures that identify design issues and improve end-product efficiency.
- Cost-efficiency for low-volume production:
FDM 3D printing solutions can be used to generate functional parts of low-volume production. The aerospace industry often requires a high level of low-volume production or custom, one-off parts. FDM 3D printing is a cost-effective solution that can produce small batches of specialised parts without high tooling, setup costs or wasted inventory.
- On-demand manufacturing and supply chain flexibility:
FDM 3D printing facilitates on-demand manufacturing, producing parts as needed, allowing aerospace companies to have flexible supply chain management. FDM 3D printing can produce spare parts on-demand and on-site, eliminating the need to rely on external suppliers and reducing lead times.
- Aerospace certification and accreditation:
The most advanced aerospace companies, OEMs, material suppliers (including Stratasys), and regulatory authorities have collectively established industry standards and regulations for aerospace FDM 3D printing. FDM technology has advanced to incorporate high-performance materials that meet stringent aerospace standards and certifications for strength, durability, and other critical properties.
- High performance and quality components:
The aerospace industry is one of the most challenging markets for 3D printing, as components have to be both strong and lightweight. FDM 3D printing meets both of these requirements by producing flight-ready aircraft parts made of high-performance thermoplastics and carbon fibre reinforcements that stand up to rigorous testing and high-stress environments, such as ULTEM™ 9085.
ULTEM™ 9085 is a high-performance thermoplastic material formulated for use in high temperature 3D printing processes (FDM). Widely used in the aerospace industry for applications that require strong, lightweight, and heat-resistant aerospace components that would be challenging to manufacture using traditional methods , ULTEM™ 9085 allows for the creation of complex geometry and lightweight structures.
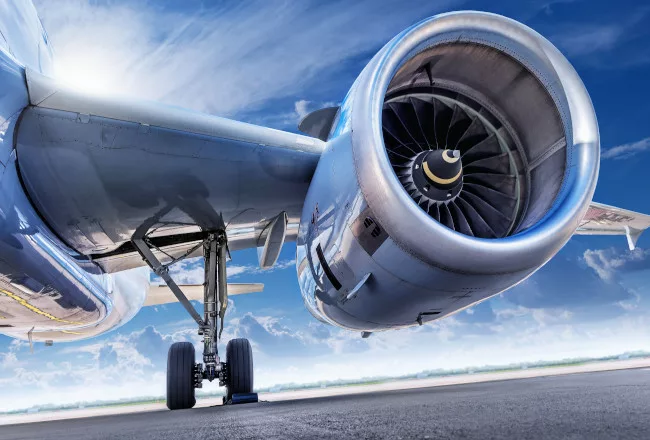
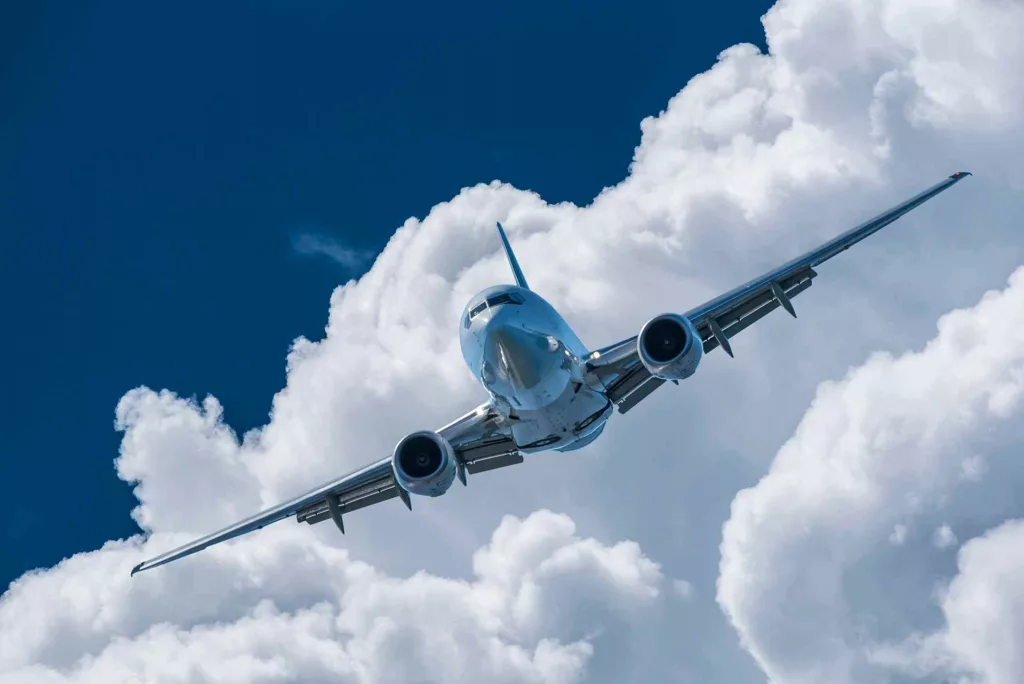
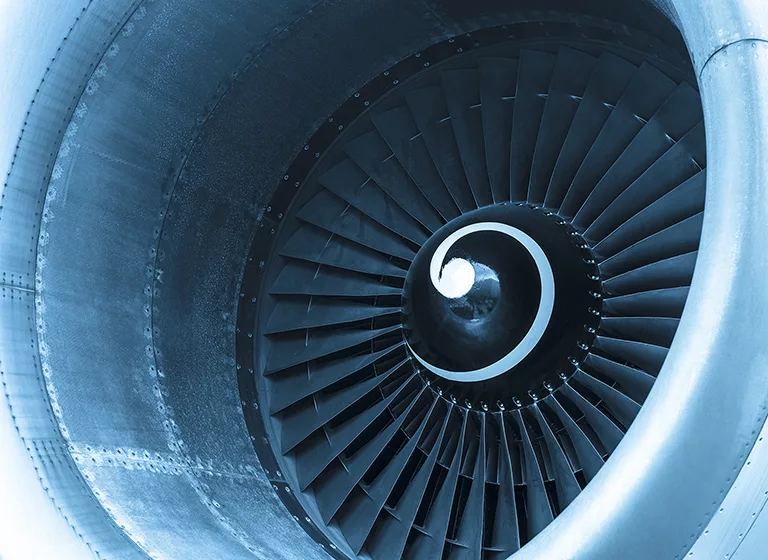