White Paper
A guide to additive manufacturing for custom metal form tooling
This white paper presents the findings of a case study involving the use of FDM additive manufacturing to create custom sheet
metal form tooling. The design and processing techniques are specific to this use case but can be applied to most metal form tooling applications.
Get your copy today to discover a complete application overview and how to achieve the best possible results for custom metal form tooling across the entire industry.
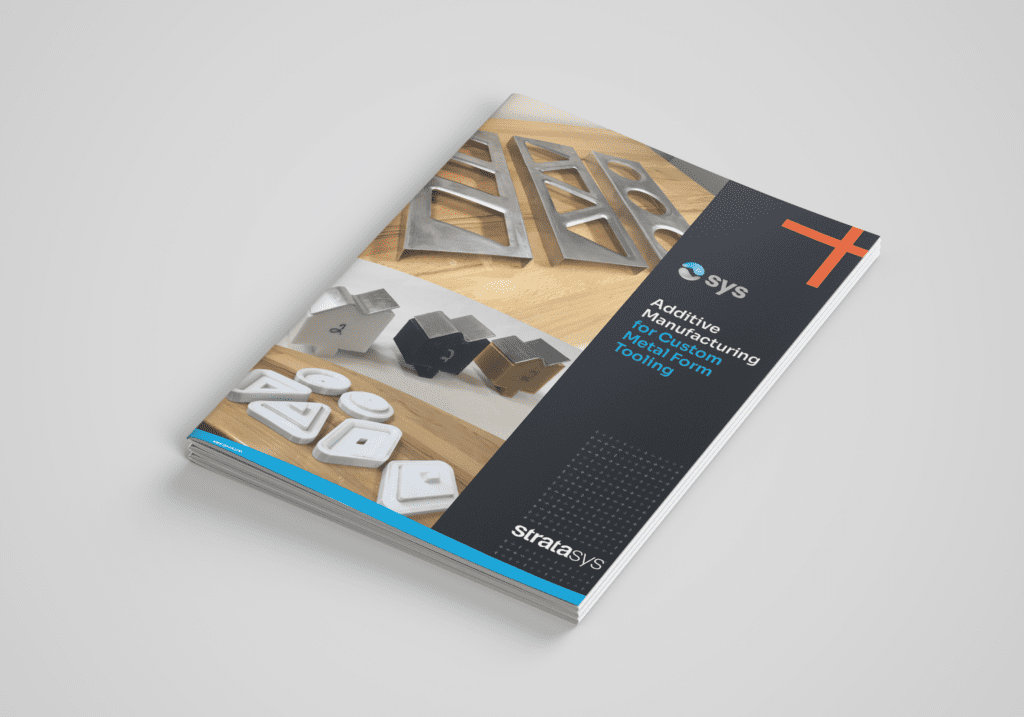