What is SAF 3D printing?
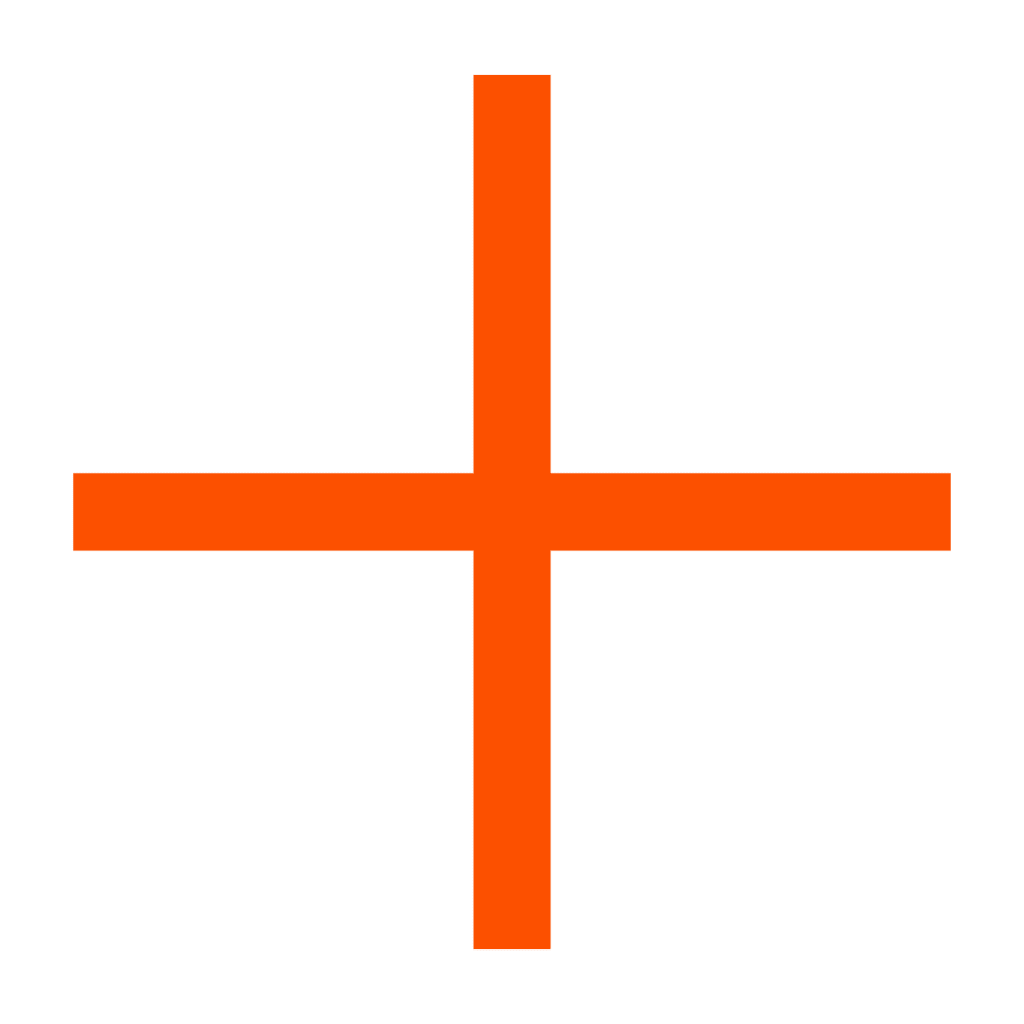
SAF technology or Selective Absorption Fusion uses an infrared-sensitive HAF (High Absorbing Fluid) to fuse particles of polymer powder in discrete layers to build parts.
Stratasys SAF technology uses Big Wave powder management, a proprietary technology that includes powder distribution across a bed, where industrial-grade print heads jet the fluid in prescribed areas to create each layer of the part.
This is followed by exposure to infrared energy, which causes the areas with HAF to melt and fuse. The sequence is repeated until the parts are completed.
SAF technology empowers a powder-based additive manufacturing process that employs industrial-grade technology to achieve higher levels of production of end-use parts.
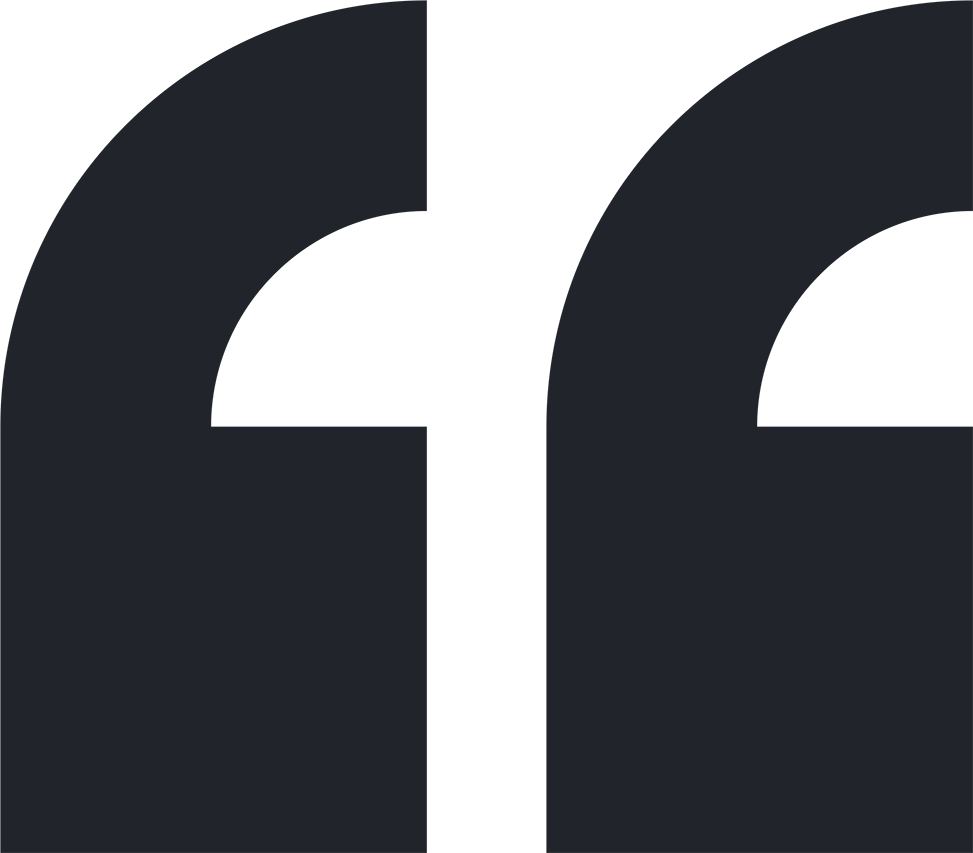
We have fulfilled orders for large parts as well as bigger orders for smaller parts and are impressed with the performance of the SAF technology.
Philipp Götz - Götz Maschinenbau
Key benefits of SAF technology
Industrial-grade technology
A cost-effective method for printing functional prototypes, manufacturing aids and high-value, low-volume projects.
Production throughput
One-pass print and fuse, few consumable replacements for minimal downtime and high-nesting densities to meet production demands.
End-use production parts
Real-time powder heating, unique thermal management and broad powder range for a wide spectrum of part properties.
SAF technology
Putting additive manufacturing on a new level
Learn more about SAF technology and how it removes the barriers to higher-volume additive manufacturing production. You can discover the Stratasys H series and how it is making mass production easier, quicker and more flexible.
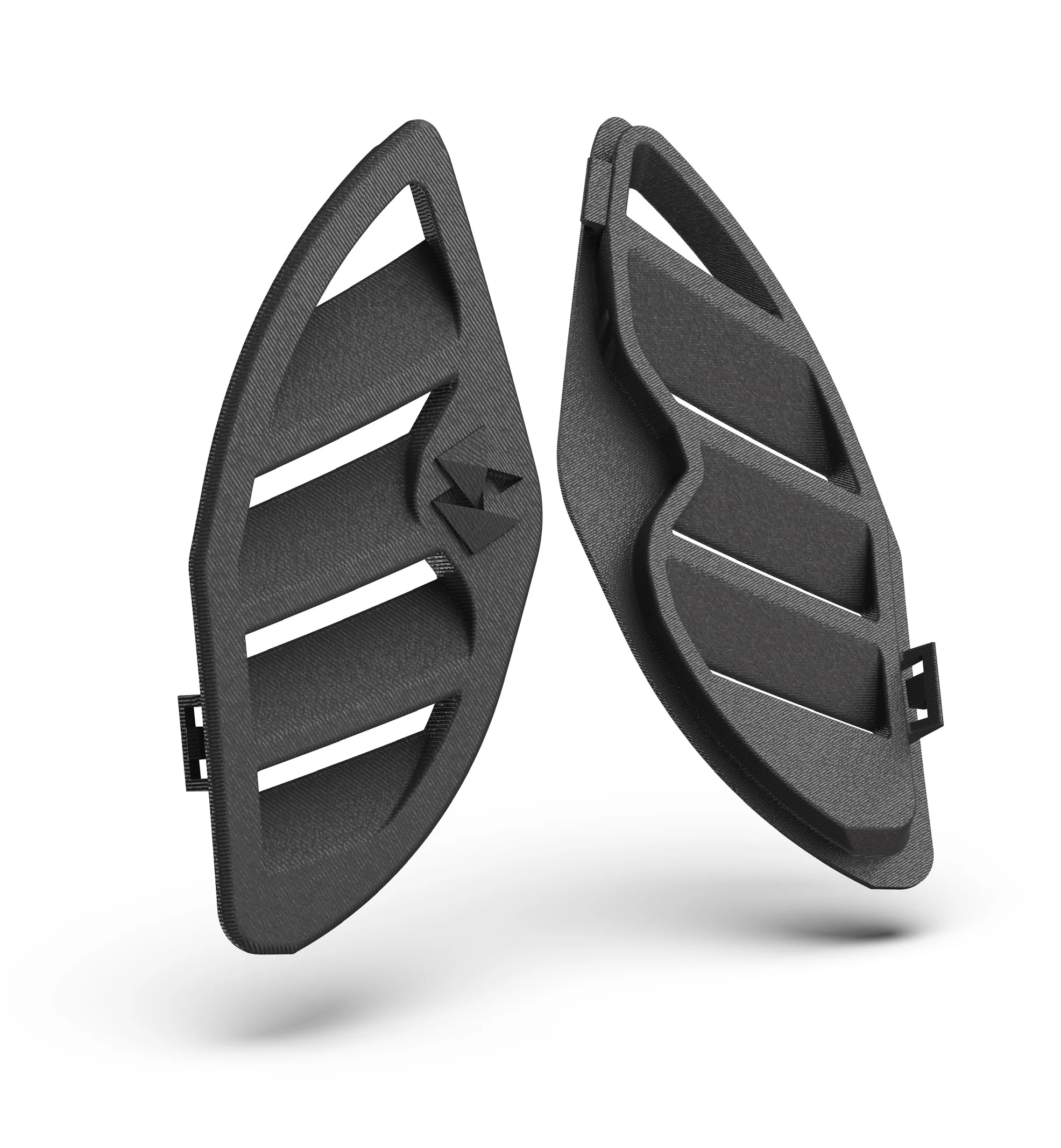
Filament materials
In FFF processes, materials are extruded through a heated nozzle and deposited on a build platform to form an object. In SAF, materials are formed into droplets and absorbed by airflow into the build platform. This allows finer control of the materials used in the process.
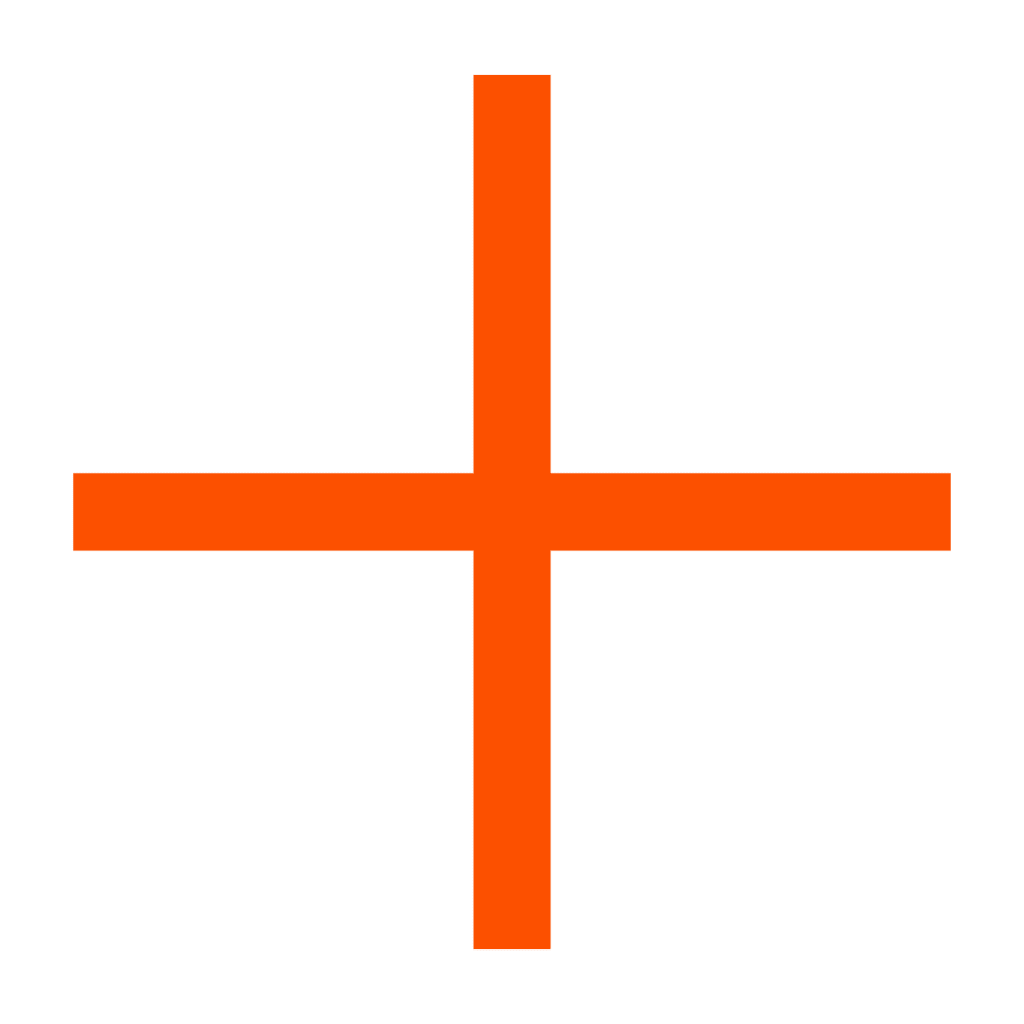
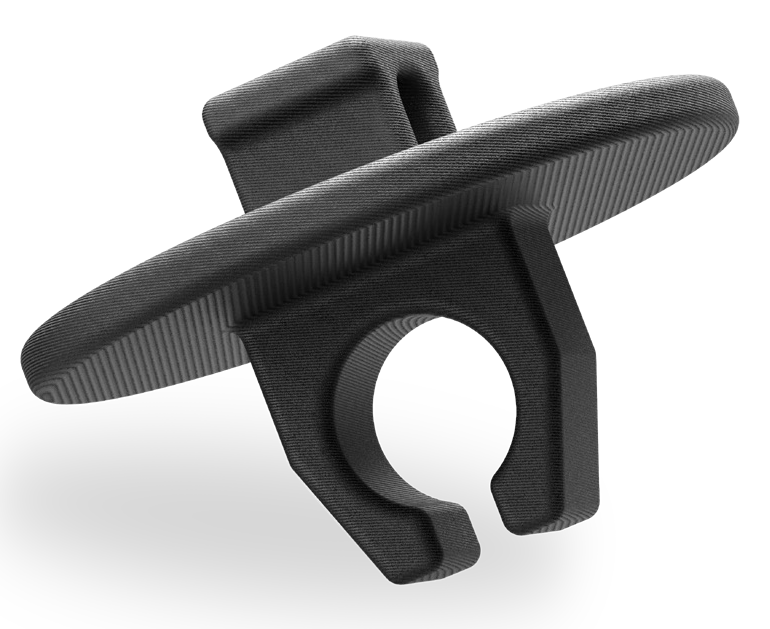
Decreased cost
Because the polymer is not melted in the hot end nozzle prior to extrusion, the plastic must be melted in a separate melting zone, such as a water bath or extruder. This reduces the need for expensive equipment required to melt the materials at high temperature.
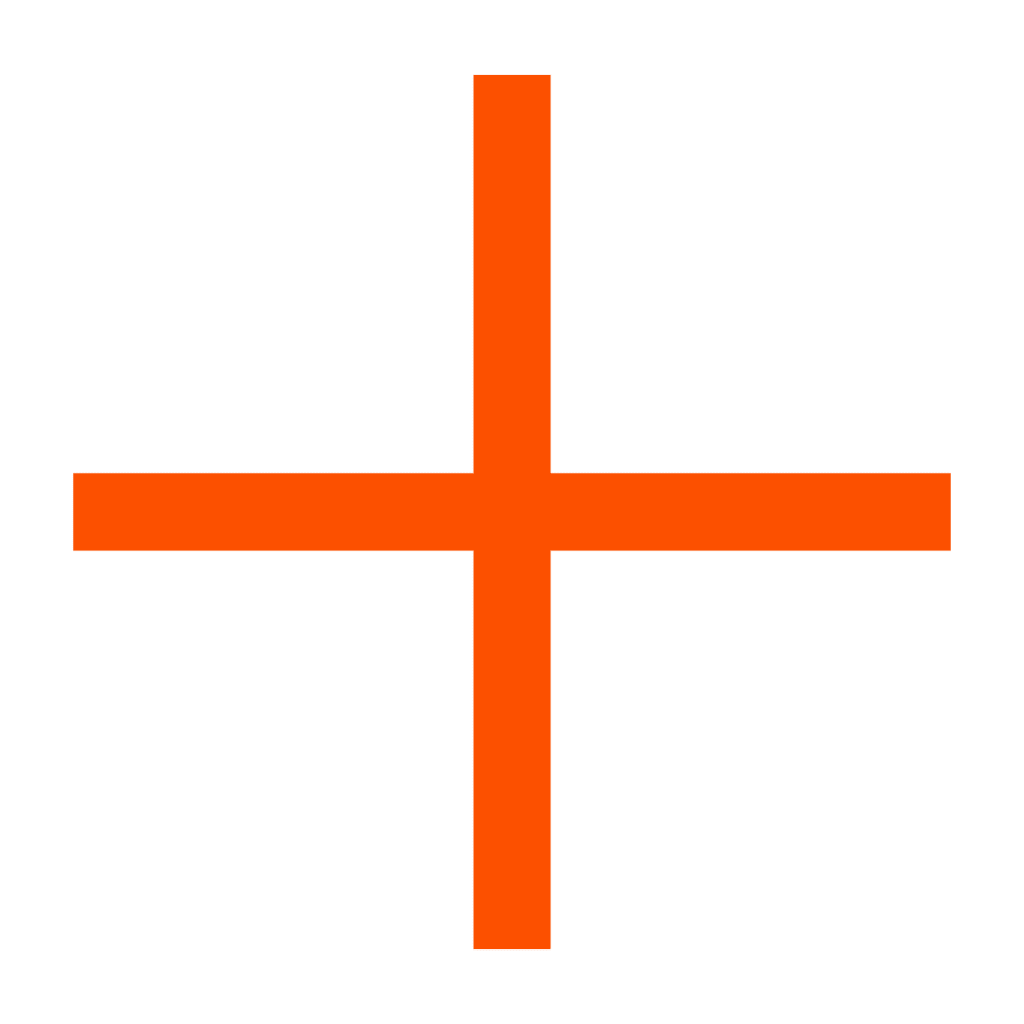
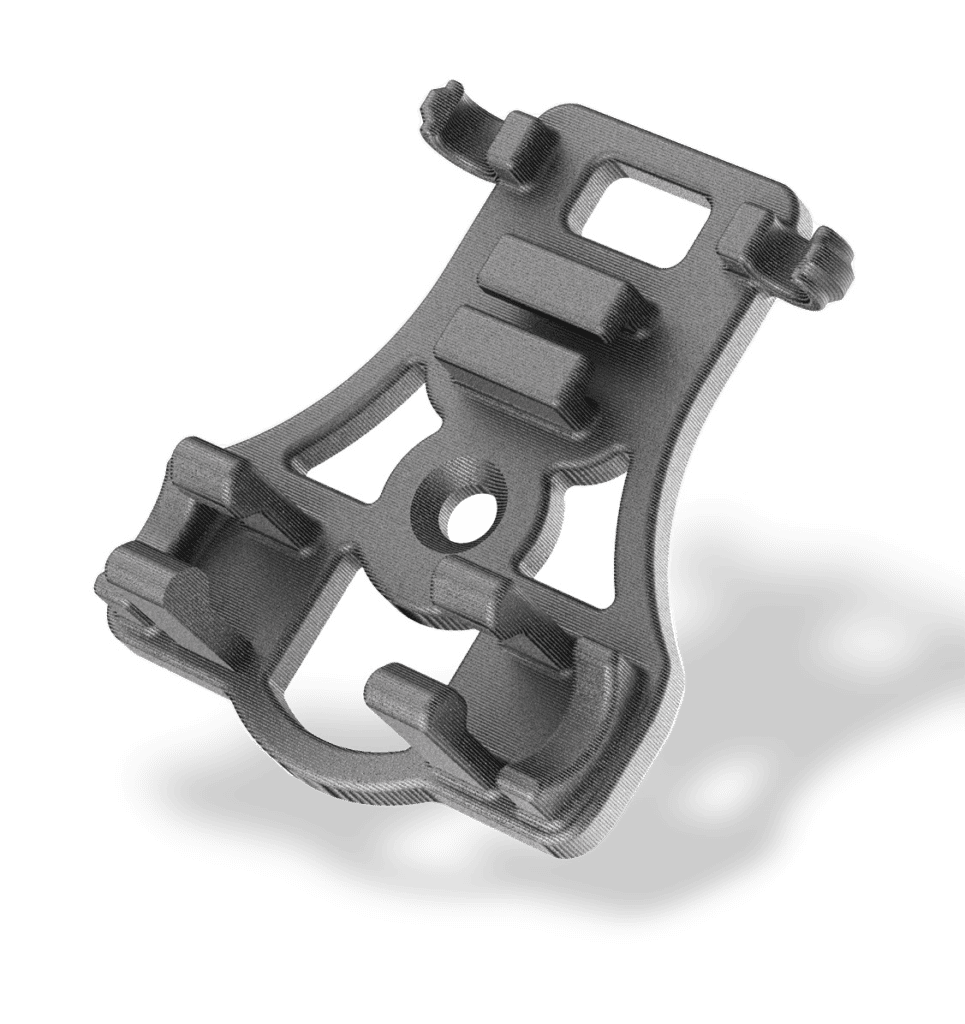
Improved speed
Polymers absorb energy much quicker when heated to very high temperatures than when they are heated at lower temperatures, which improves overall printing speed and throughput. It also allows for faster heating and cooling cycles to minimise distortion.
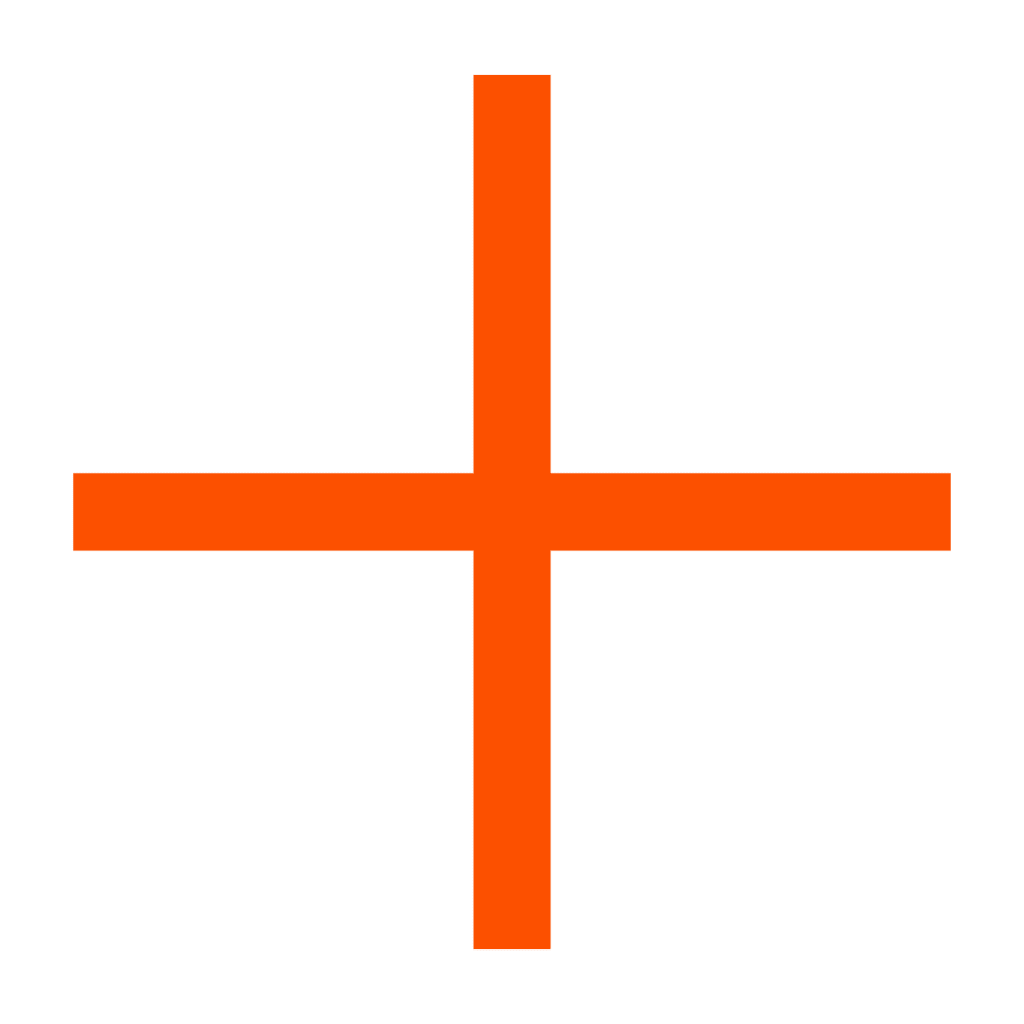
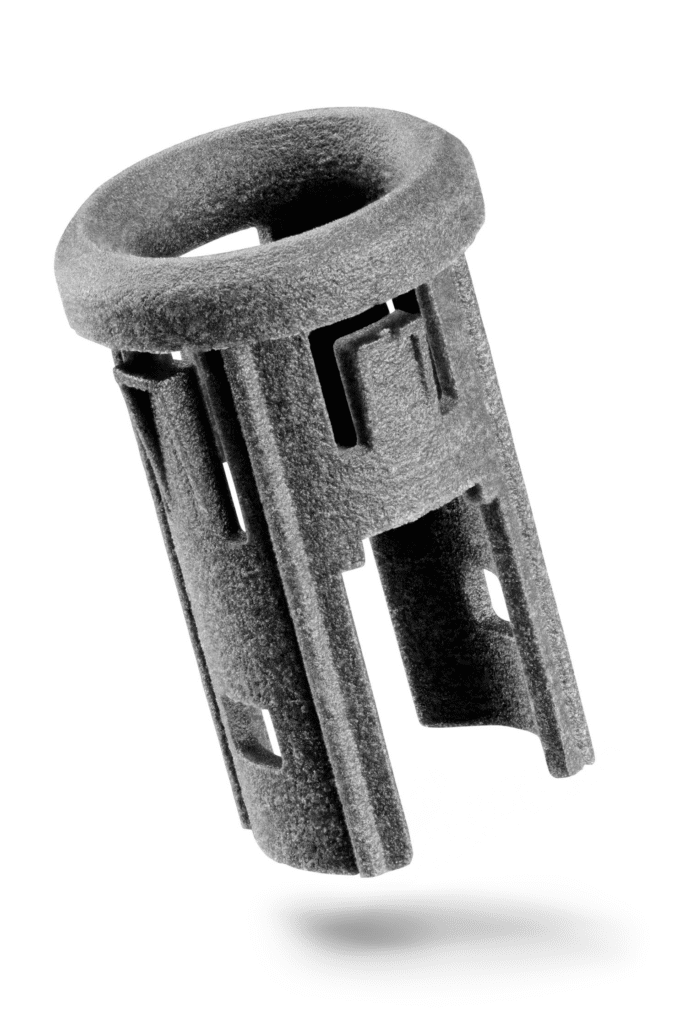
High resolution
Since the polymer droplets are absorbed by the airflow, there is no pressure drop associated with this technique so the air can be re-circulated without slowing the process down. This eliminates the need for an additional air compressor and increases the overall efficiency.
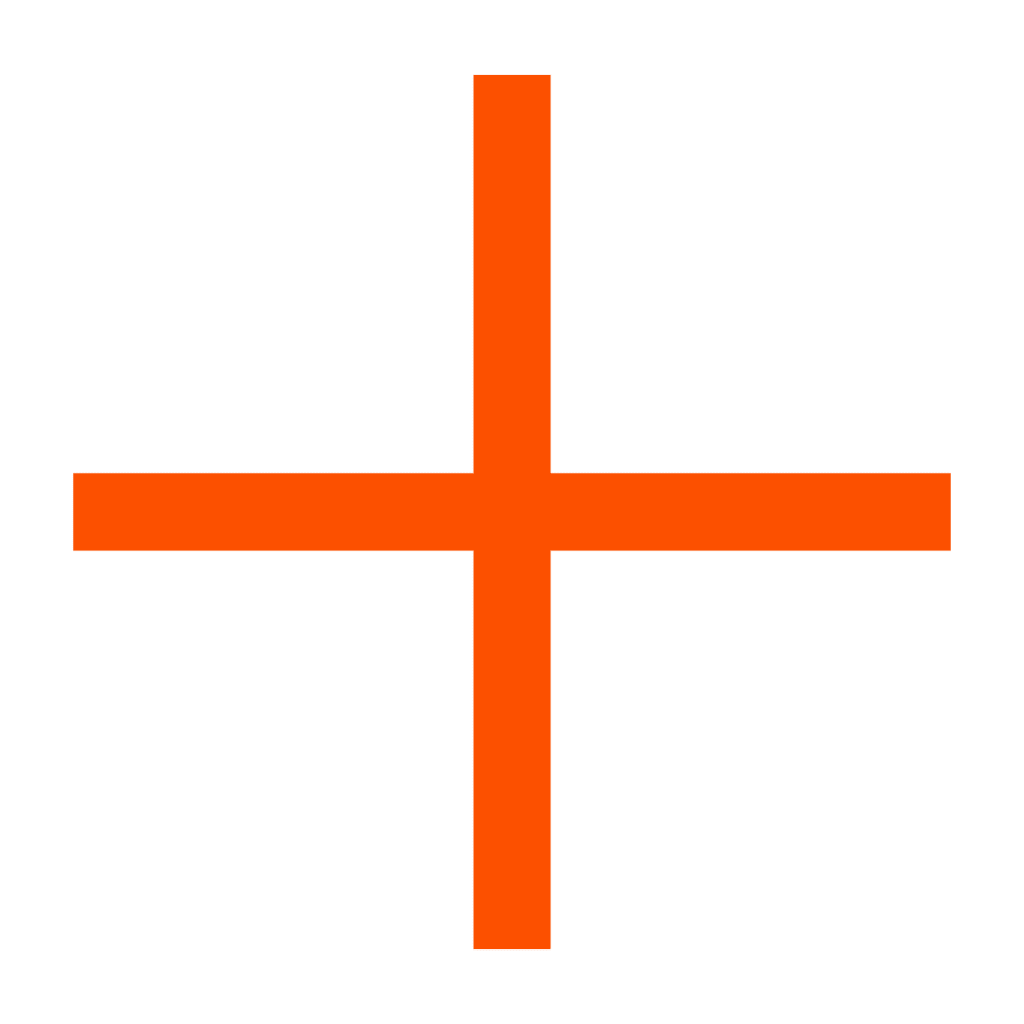
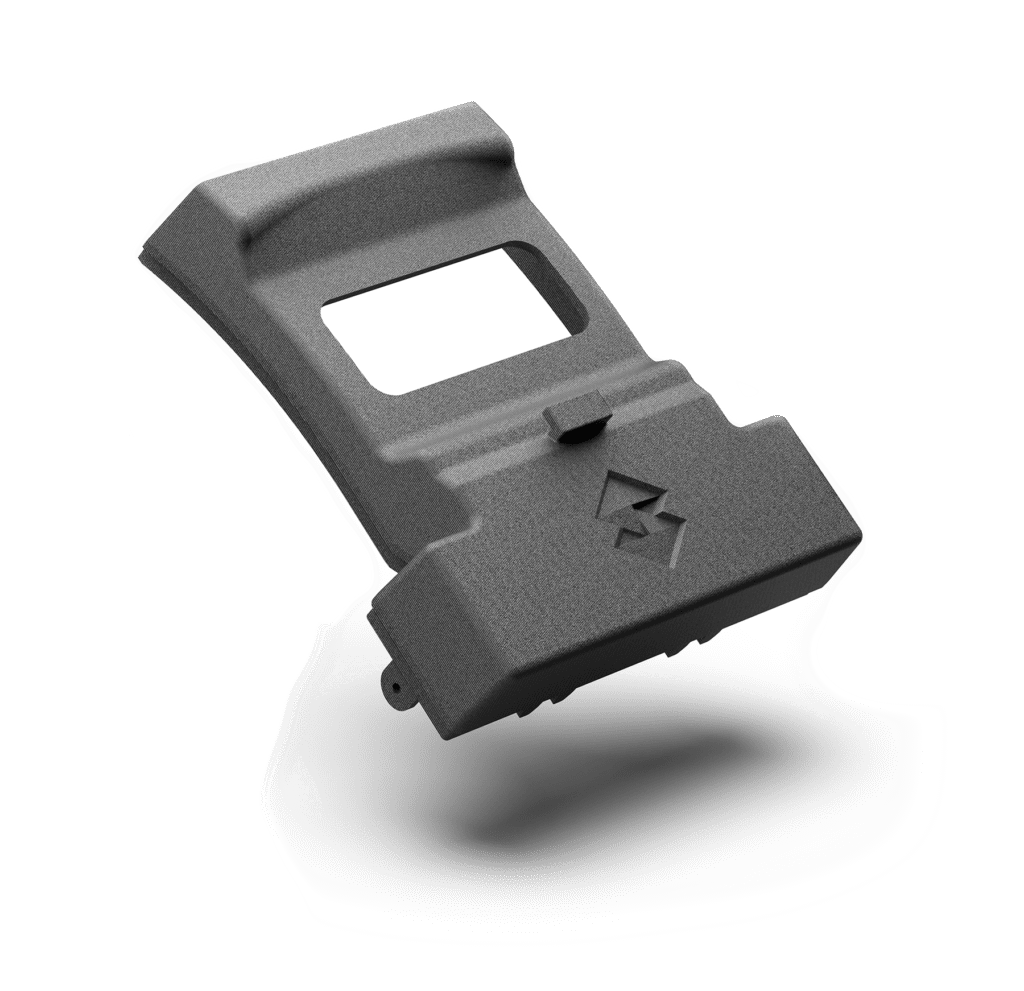
SAF FAQs
Polymers absorb energy much quicker when heated to very high temperatures than when they are heated at lower temperatures, which improves overall printing speed and throughput. It also allows for faster heating and cooling cycles to minimise distortion in printed parts due to residual thermal stress. Because 3D printers print optimally when the heat is consistently high, SAF saves time and money on other processes due to requiring a lower temperature to print and ultimately get printing.
Plastic materials that are printed using powder bed fusion 3D printers typically have much stronger mechanical properties than those that are printed using other additive manufacturing processes such as SLA.
The prints are very durable. Owing to the quality materials and printing techniques used, the print should hold up well over time. This includes exposure to water, sunlight, heat and other potential hazards.
SAF printers are designed with a high resolution that helps to minimise surface defects and roughness, ensuring that the quality of the part remains high.
SAF 3D printing provides extremely accurate results. This is due in part to the printing technique itself as well as the superior materials used in the printing process. The printer incorporates multiple processes to ensure a high-quality print every time. The materials are also specially designed to produce highly-accurate prints that adhere to the original design.
For rapid prototypes, the cost will be low as once the design is finalised the final product is produced quickly and at a lower cost than if printing would be done by hand or using other prototyping methods. Costs for printed objects in a production environment are very low; it is far cheaper to print a large item than to produce it using other methods such as injection moulding or CNC machining.
Some post-processing operations may be required depending on the part design and/or the material being used. This could include removing excess powder, bead or sand blasting, and vapour smoothing. Due to the nature of the process, however, these operations are typically much less invasive than those required in other printing techniques.
High-resolution 3D prints take approximately four hours to print. This can vary based on the size of the model being printed.
SAF 3D printing technology works using powder-based materials to create solid objects. SAF printers fuse layers of powder together to create 3D models. Compared to other printing techniques, this method can produce more complex and durable prints in less time. The material used in this process is engineered for precision and durability.